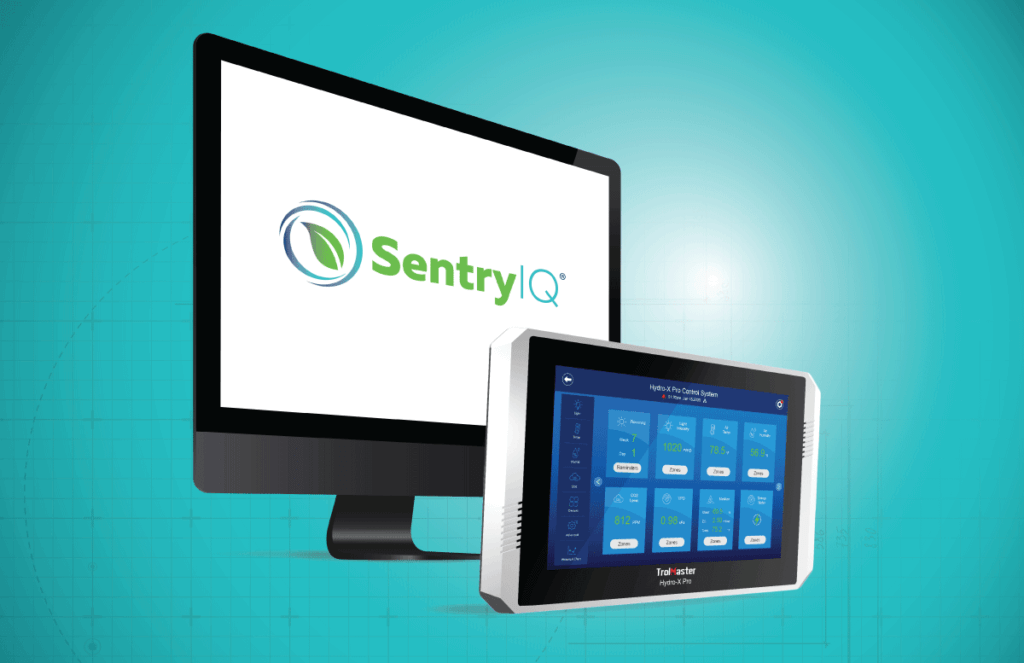
Grow room environment controls for agriculture
Take control of your indoor farm. Surna Cultivation Technologies offers a variety of options for monitoring and managing grow room temperature, humidity, CO2, irrigation, lighting, and more.
Get a custom controls and automation solution designed specifically for your grow facility with SentryIQ. Or, select a modular plug-and-play option with our TrolMaster offerings.

SentryIQ®
Grow smarter with this sophisticated, custom indoor cultivation facility controls & automation system.
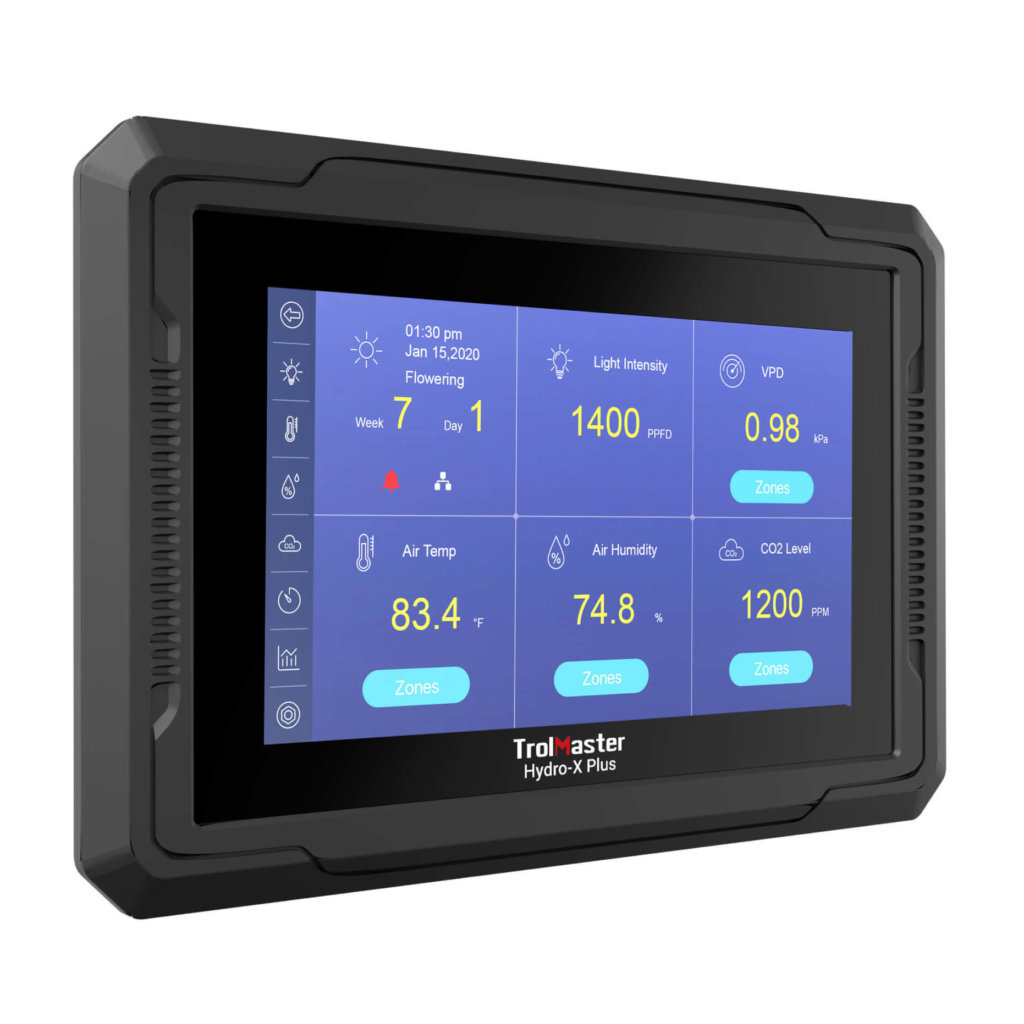
TrolMaster
Explore Surna’s selection of TrolMaster modular control systems for climate, lighting, irrigation, and CO2.
3 Easy Steps to Get Growing
Contact Us
We’ll have a brief discussion about your facility and the goals you are looking to achieve with it.
Review Your Options
We’ll clearly articulate the cultivation system options available to you to help make your decision process easier.
Receive a Solution
You’ll receive a customized solution to meet your specific goals.
Solid Engineering, load calcs are always on spot on.
I have had very good experiences collaborating with Surna as being both the equipment supplier and Engineer of Record on a large cultivation project...together we worked through a number of project issues that saved the Owner both time and money
Contact Us
Ready to get started or learn more about how we can help your facility succeed? Fill out the form and a company representative will be in touch.
Contact Us
Ready to get started or learn more about how we can help your facility succeed? Fill out the form and a company representative will be in touch.