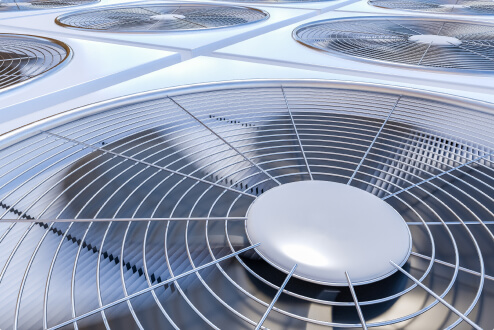
We’ve often referred to the importance of HVAC systems to every layer of the cultivator’s business, but how do you choose which approach is right for your facility?
The truth is, there are a number of technologies that can successfully manage the climate in an indoor facility. One of our most important responsibilities as your design partner is to review with you all options in depth, along with budgets and their respective pros and cons, to assist with the decision-making process. Your goals, not ours, inform the design process. Our job first and foremost is to understand your goals, and then to design a system that best meets those goals. There is no substitute for a conversation with one of the experts on our team and the wealth of knowledge that comes along with it. If you’re not ready to call us quite yet, you can find a summary of some of the HVAC-D technologies in which we specialize below.
3 Easy Steps to Get Growing
Contact Us
We’ll have a brief discussion about your facility and the goals you are looking to achieve with it.
Review Your Options
We’ll clearly articulate the cultivation system options available to you to help make your decision process easier.
Receive a Solution
You’ll receive a customized solution to meet your specific goals.
Standalone Systems
In variable refrigerant systems, refrigerant volumes are modulated and distributed to multiple areas of the building depending on cooling needs at any given time. With this type of system, multiple fan coils or air handlers can be connected to a single condenser, allowing condensing units to be shared between spaces without sharing air, (similar to chilled water systems with slightly less flexibility). The ability to modulate refrigerant based on current cooling requirements and move cooling to areas of the building that need it result in a very high listed EER, although this is based on comfort cooling applications and cultivators are unlikely fully capitalize on the high efficiency ratios due to the largely constant cooling load in most cultivation facilities. Temperature is controlled by air handlers or fan coils and dehumidification is controlled by separate, stand-alone dehumidifiers. This approach may be a good option for cultivators seeking an improvement in energy efficiency and redundancy over standard light commercial HVAC systems, or cultivators whose authority having jurisdiction are calling out a specific EER for regulatory compliance.
Technology Options:
- Low ambient kits
- Multiple air handler/fan coil configurations
- Ground or roof mounting options
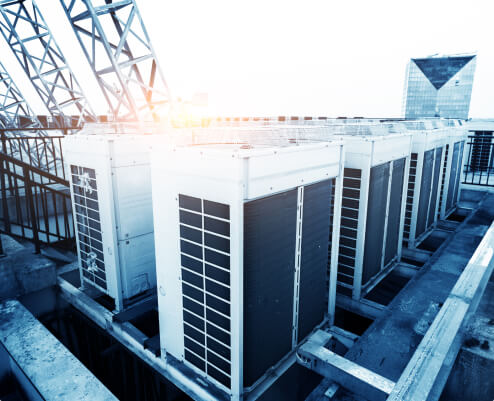
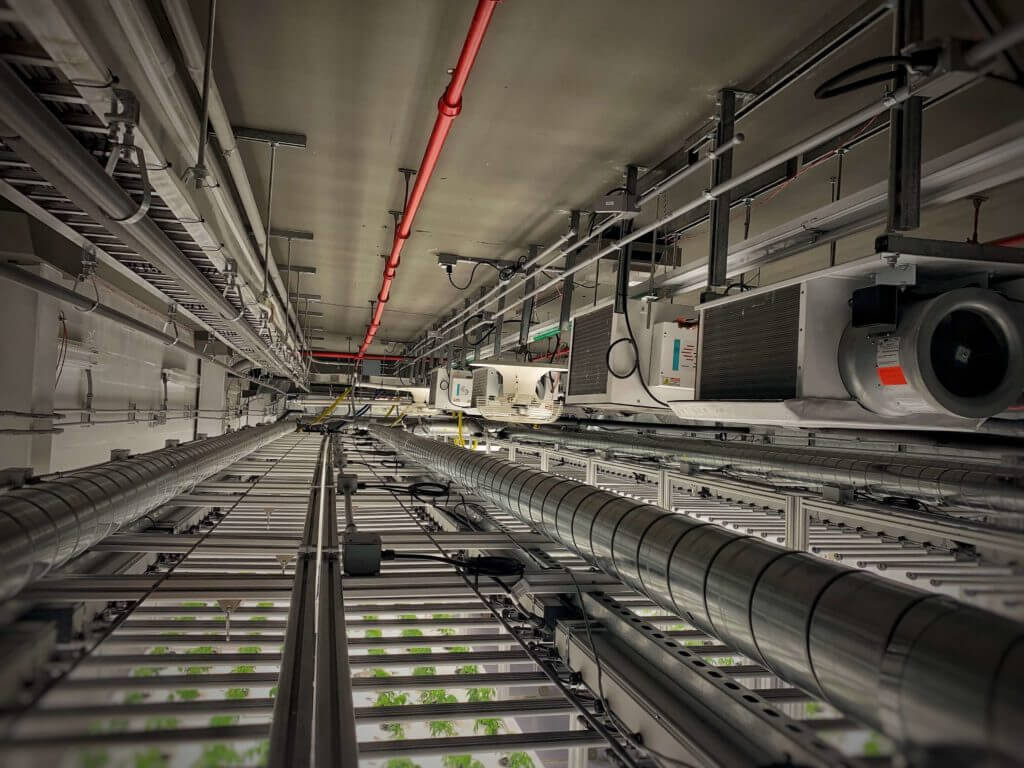
Technology Options:
- Extreme low/high ambient operation
- In colder climates, substantial free cooling opportunities (with or without ventilation)
- Ducted or ductless air handler options
- Affordable custom air handler configurations for spatial or structural constraints
- Ground or roof mounting options
Integrated Systems
Hot gas reheat systems are refrigerant based, DX systems, designed to integrate cooling and dehumidification operation within a single system. This allows for greater precision than with stand alone dehumidification systems, and reduce or eliminate the need for additional, stand alone dehumidifiers, which can improve energy efficiency and reduce electrical infrastructure requirements. In these systems, the refrigerant circuit is routed through the airstream twice—once to remove BTU’s (heat and humidity) from the air, and then to replace the heat back into the airstream to make dehumidification operations temperature neutral (or allow for dehumidification when temperature modification is not needed). Integrated controls manage the flow of refrigerant, allowing for a relatively simple front-end controls interface. Longevity is generally superior to standard, comfort cooling-style DX systems as these systems are intended for cultivation applications, while installation requirements are similar to standard HVAC systems. These types of systems are a good mid-range cost option between cost, electrical infrastructure and complexity, where energy efficiency and longevity are generally superior to stand alone systems.
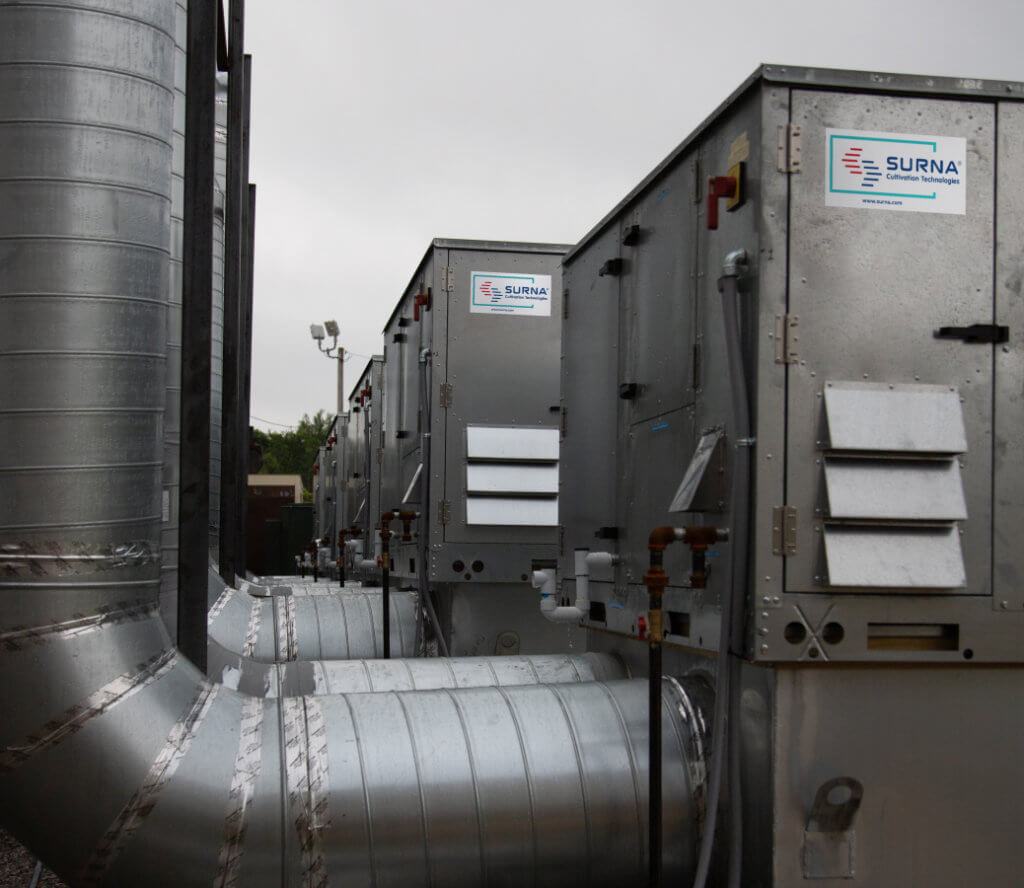
Technology Options:
- Modulating Hot Gas Reheat for greater precision
- Ducted or Ductless air handling options
- Affordable custom air handler configurations to accommodate special climate needs or spatial/structural constraints
- Low ambient kits
- Heat pipe technology to reduce connected load and energy consumption
- Desiccant technology to enhance dehumidification capacity and reduce connected load and energy consumption
- Ground or roof mounting options
Testimonials
With Surna products, we've seen much more stable temperature and humidity and our plants are happy with the consistency.
In the numerous times I have worked with the Surna team, I have always been satisfied with the quality and service I received.
Even when project issues developed that were not Surna’s responsibility to deal with, the Surna team was more than willing to come to the table to help with resolving these issues.
We’ve always recommended the Surna system for as long as we’ve had it because it’s just another thing we don’t have to worry about.
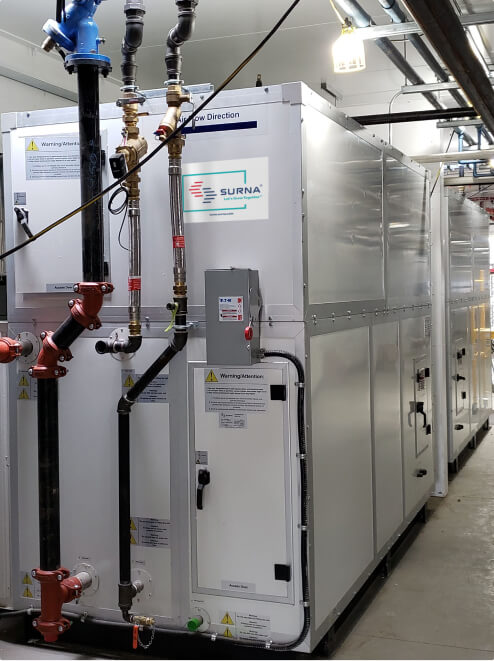
Four pipe chilled water describes a system in which chilled water is the primary mechanism for heat exchange for both temperature and humidity management. The airstream is routed first across a chilled water coil to remove heat and humidity, followed by a reheat coil to ensure temperature neutrality when operating in dehumidification mode, which allows for substantial reduction or elimination of stand alone dehumidifiers, improving energy efficiency and reducing electrical infrastructure requirements. Reheat is accomplished through heat recovery chillers, reusing the heat produced by cultivation operations, with boilers as back up. With this type of approach, air handling systems operate independently of the compressors, allowing one central plant to operate multiple rooms without mixing air between rooms, allowing for further reductions in electrical infrastructure as well as cost effective redundancy. Four pipe chilled water utilizes a sophisticated controls system, which provides visibility into every area of the climate control system, allowing for significant data analysis by the cultivation team as well as by the engineering team to fine tune the system to ensure maximum precision with minimum energy consumption. These systems usually result in the tightest precision, most redundancy, highest flexibility (in both air handling options and achievable results), lowest electrical infrastructure requirements, and longest overall lifespan of all available options. Four pipe chilled water is the preferred option for cultivators for whom the maximum precision, flexibility, and insight into facility operations are a high priority.
Technology Options
- Ducted or Ductless air handling options
- Affordable custom air handler configurations to accommodate special climate needs or spatial/structural constraints
- In colder climates, substantial free cooling opportunities (with or without ventilation)
- Extreme low/high ambient operation
- Heat pipe technology to reduce connected load and energy consumption
- Desiccant technology to enhance dehumidification capacity and reduce connected load and energy consumption
- Ground or roof mounting options
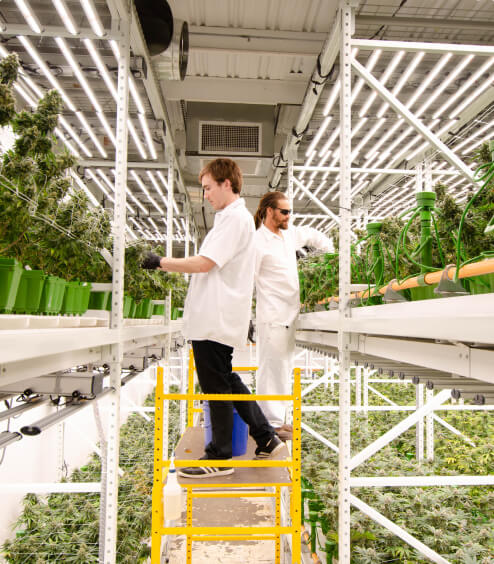
Contact Us
Ready to get started or learn more about how we can help your facility succeed? Fill out the form and a company representative will be in touch.