Watch the Recording
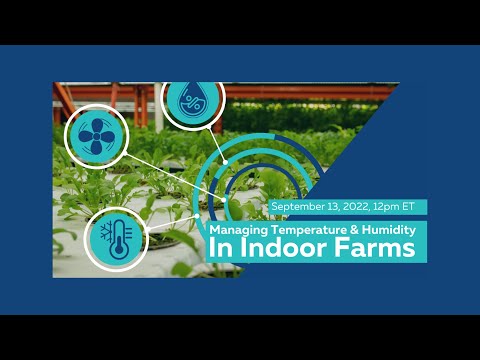
When it comes to climate control, maintaining an adequate environment for your plants is far more complex than heating or cooling a building for human comfort. The temperature and humidity of your grow will have a direct impact on your crop’s health and yield, so it’s important to get it right.
Surna Cultivation Technologies Co-Founder Brandy Keen and Application Engineer Ian Atkins, P.E. join Agritecture Systems Engineer Alberto Lopez and Lisanne Meulendijks, Global Research & Development Director at Kalera in a discourse on managing controlled environment agriculture climates. Topics include:
- Humidity, VPD, and Dehumidification
- Cooling and Heating
- Airflow
Interested in how Surna’s can help your grow facility succeed? Contact us today!
This webinar was recorded on September 13th, 2022. The recording is available for free on YouTube.
More Resources on HVAC Approaches for CEA
Enjoyed our panelists’ discussion the components of managing controlled environment agriculture climates? Dive deeper into the various HVAC technologies used in CEA and begin finding which approach may be appropriate for your specific climate. Download the free white paper today.
Transcript
[Brandy Keen] I appreciate everybody jumping on and joining us today. My name is Brandy Keen, I am the co-founder and senior technical advisor for Surna, and what Surna does is architectural design and MEP engineering specifically for cultivators with special expertise in climate control systems. After 16 years or so of doing that kind of work, I have learned quite a bit and I’d like to say I have a little bit of experience in that field, but to be quite honest, the experience that I have pales in comparison to the panel members who are joining us today, and I’m really excited to have them with us, and am frankly honored that they would join us. So what I’d love to do is have them introduce themselves, starting with my colleague Ian Atkins. Jump on and tell us a little bit about you.
[Ian Atkins] I’d love to, thanks Brandy. I’m Ian Atkins with Surna. At Surna, my role is application engineer, so I focus on applying our products and systems to indoor agriculture projects. Largely, I focus on sizing the systems – how much cooling is needed, how much dehumidification is needed – then also pricing them and then oftentimes working to get them tuned in and working optimally once they’re started up. I’ve been with Serena for about three years now and worked for about two years for another engineering consulting firm also in CEA focused on HVAC.
[Keen] Awesome, thank you. Speaking from direct experience, you’ve had enormous value for our clients certainly. Alberta what about you? Would you like to tell us about yourself?
[Alberto Lopez] Sure! Hi everyone. My name is Alberto Lopez. I’m assistant engineer for Agritecture – I guess you guys know what Agritecture is. Basically, what we try to do is to help entrepreneurs build their projects, assess, and plan and to see what are the resources needed to fulfill the project. My background is agricultural engineering, I’m originally from Costa Rica, and I’m based in Amsterdam. I came to the Netherlands to study biosystems engineering. Both my degrees focus more in climate control strategies and before Agritecture, I worked in the first vertical farm in Amsterdam for around three and a half years, and I’ve been with Agritecture for around three years and my main roles are to assist the technical team to assess the resources, let’s say energy, water, CO2, consumables for the visibility of a project.
[Keen] So much experience on this panel – it’s really exciting. Last but absolutely not least, Lisanne.
[Lisanne Meulendijks] Hi there everyone! It’s amazing to see so many of you joining from across the world. I appreciate the invitation to join this panel discussion. I’m Lisanne Meulendijks. I’m the global R&D director of Kalera. For those who do not know Kalera, Kalera is a large vertical farming company. We actually are an operational Farm – well, farms. We have several large-scale facilities across the globe; several in the US and also in Kuwait and ramping up our large-scale facility that is going to be in Singapore. Our offices are also based across the globe – I officially work for the Munich office but I’m based in the Netherlands close to the heart of the horticulture industry here. And in my role as Global R&D director, I focus on continuously improving the cropping strategy in our existing Farms by running R&D trials in the different R&D locations that we have. I also work on new product developments, but an important part of my role as well is as translating the crop requirements to our engineering team, and together with the engineering team to find the technical characteristics of our future farms and of upgrading our existing farms. I really have a strong focus on understanding the interaction between the crop and the technical installation and how does the crop in influence its own environment, and , that’s my specialty. I have a background in bioscience engineering, focused in agricultural Engineering in my masters that one year of my PhD but that moved into the field of vertical farming – first in the commercial vertical farm and then in a consultancy company that provided knowledge as a consultancy service, and over half a year ago joined Kalera as a global R&D director.
[Keen] Thank you guys very much! As you can see, we have a wide range of expertise both on the design side of things and on the application side of things so again really excited to have to have the three of you with us today. For the folks joining us, I think that it’s important to point out how important climate management is in cultivation operations and that it’s really going to touch every layer of your business financially from Capital expenditures to operating expenditures to revenue and yields, so I’d like to start there with you Lisanne, and can you give us a high level overview of the importance of climate management what the impact is on the crop? I think we talked about survive versus thrive versus steer.
[Meulendijks] Actually what I’ve seen in this industry is that it’s extremely important to understand and optimize your climate conditions, but it’s also extremely challenging. And when this journey started for myself, I was running R&D trials on a very small surface in a one layer system, and then I experienced that scaling up R&D results into a multi-layer, highly packed climate zone is actually quite a challenge, and this challenge kept recurring, and also today is still a challenge as well, you see that once you start squeezing in as many square meters of growing space as possible in a certain room in a certain volume, the impact of your crop on the climate increases. And it’s a very important and crucial in the design stage already to try to quantify this impact and take it into account and from experience I see that it’s often in a design stage already underestimated. For example dehumidification capacity, how much airflow do you need to actually create the climate also inside the canopy of the crop, and when that is not optimally designed, let’s say we see huge challenges with crop quality and yields and the one big issue on top level is the burn – I think most of you are familiar with that challenge. So for me as a grower, from the grower perspective, it’s always find that sweet balance between having a high growing speed and avoiding … so you’re constantly looking for that boundary because we’re pushing boundaries in this industry, we’re not here to grow comfortably. But the crucial factor there is having a good climate that enables for those higher growing rates and a good climate meaning avoiding, for example, 100 humidity levels around your crop, but also understanding at which points during the day cycle, for example, which humidity levels are accepted and how strong the slope should be so it’s more than just a day and night temperature set point, it’s really understanding the interaction and avoiding risky moments across the whole day cycle. And that likely leads to not-too-good quality crops and then hands also higher yields because that’s of course what we’re aiming for: high quality, high yielding product.
[Keen] You have the component of we need to keep things within a certain parameter to avoid disaster, but then we can also optimize further to actually promote higher yields and even better quality if we manage it correctly and collect the right data and understand what minor adjustments we’d like to make.
[Meulendijks] Yeah exactly. And growing crops is a biological process and actually quite predictable. If our yield is created by photosynthesis which is for which we need the LED lights to be on and the plants can handle a certain DLI (daily light integral) depending on how well the climate is, so in case I have a difficult climate to cope with, one of the main rules that that exists are lowering your DLIs, the amount of light you give per day, so you’re slowing somewhat that growth speed and you’re on the safer side of getting into … but that comes of course at the expense of how many days you have to pop inside. So there’s a correlation between those two.
[Keen] So you may be able to work with it, but you have to compromise in ways that may not be optimal. You mentioned, Lisanne, humidity, and it’s timely because I was actually gonna ask you next – you mentioned that there are challenges obviously in a number of ways with maintaining the climate in a cultivation environment, one of those obviously being humidity. And temperature and humidity interact with each other in a lot of ways that may increase the challenge when you’re doing those load calculations. Ian, can you give us a little bit of information about how temperature and humidity interact with each other and why that’s challenging?
[Atkins] Definitely. One thing about grow rooms is that you’re usually trying to control both the temperature and the humidity and a lot of comfort applications you’re just controlling the temperature. As Lisanne mentioned, in grow rooms there’s also usually a really high latent load from all the moisture that the plants are giving off, and so you have to balance the latent load coming out from the plants with how much you’re removing it. And how that interacts with the climate is warmer air – or one way to think about it, you could talk about this in a lot of different ways, but one way to think about it is that warmer air can hold a lot more moisture than colder air and so what that does is potentially at warmer temperatures in a lower humidity as it can dry cause the plant to transpire more, but then also on the equipment side, warmer temperatures are generally easier to pull a lot of humidity out of because there is a lot of moisture in the air, whereas at cooler temperatures, because there’s not so much moisture in the air and we’re generally removing moisture just by condensing it, on a cold surface it’s much harder to remove the moisture from colder air that’s closer to the temperature of a cooling coil. So that’s one way that temperature and humidity interact in the grow room between the system and the plants.
[Keen] So when you’re aiming for a cooler temperature and a lower relative humidity, you may not get as much output out of your system as when you’re aiming for a higher temperature and a higher relative humidity for instance.
[Atkins] Definitely, yeah.
[Keen] And then that’s compounded by the amount of moisture that’s present in the space.
[Atkins] Right, yea. And just to give an example, a dehumidifier will remove about half or maybe even a little less at 60 degrees and 60% humidity than at 80 degrees 60% humidity. It would remove about twice as much as 60 degrees and 60% and it and even one that’s meant to dehumidify at that cooler condition.
[Keen] So the output of that equipment is really predicated or dependent on the conditions in which it’s operating which is obviously one of the reasons that these things need to be engineered and these load calculations need to be carefully considered because you’re looking at how much moisture you’re pulling out but then you’re also looking at the performance of that equipment. Alberto, do you have anything to add?
[Lopez] Yeah, this is something really important to consider. The main differences between, let’s say, commercial buildings and vertical farms – that’s the point that we’re trying to address here – and analyzing and assessing several let’s say vertical farms at least six or seven years ago, they were not taking or not considering this amount of latent heat that you have to extract from the from the area. So all their designs and everything were based towards commercial buildings. So you start seeing a lot of issues of, let’s say, under dimensioning of the equipment, a lot of stress on the equipment as well, and then what’s remarkable to see is throughout this six years or seven years, or I guess a bit longer, how companies have specialized a lot in vertical farms and how to control humidity as well. So paying more attention to the latent heat based design that into the sensible heat as in commercial traditional HVAC systems.
[Keen] Yeah and I find, and I think Ian would agree, that in a lot of cases if you focus on the latent heat removal, which is the dehumidification piece, you really get enough sensible heat removal to offset your lights just by default because your latent loads are generally pretty close to your sensible loads.
[Meulendijks] Quickly over to your point, because I think that’s a very important point that nowadays people are way more aware of understanding that the plants add a certain latent load to the room. I think the challenge is still quantifying that as it’s so dynamic. We’re talking about the biological system, and once the crop grows bigger, the leaf area increases and the amount of transpiration enhance the latent load it adds to the room also increases. But how much it increases fully depends on your growing recipes, on your growing setpoints, but also the technical design – how is my airflow interacting with the crop. And so we understand we need to quantify the number, how to quantify is like the next, well I think for the industry, an important focus points to really optimize that the design step. And there’s ways to quantify it by measuring the transpiration rate.
[Lopez] Or also adding to that, it’s also noticeable how the design in vertical Farms have changed since 10 years ago, five years ago to now. Because before we were trying to control really huge volumes at once which will impact a lot or will have more stream in this point that you are making. The differences in or the dynamic control of the humidity. Now we’re seeing more and more vertical forms going into compartments, so each compartment has less volume to control, and basically more or let’s say that characteristic or pain time change it decreases a little bit. So you see a lot of companies going to lower and lower volumes even per layer control of temperature and humidity and other factors as well. So I guess we’re going through it, but we still need to assess it.
[Keen] You guys bring up an interesting point. Vapor pressure deficit is something that we haven’t really touched on a lot but is relevant – temperature, humidity, airflow, all of these things – Lisanne, can you give us a high level overview of vapor pressure deficit and what it means and how you target a VPD?
[Meulendijks] So the VPD I think it’s always good to start with distinguishing two definitions of VPD. So maybe pressure difference or deficit can be either the difference between the vapor pressure inside a leaf and the room, but sometimes also you see the term being used for that Delta of the air itself, so how much humidity can you still add to a certain air with a certain characteristics. So from a growing perspective, the VPD defines or quantifies the vapor pressure of the leaf itself which we regarded hundred percent relative humidity and the air is a very important parameter to take into account when growing because the VPD of the air actually is quantifying the strength with which the air or the climate is pulling out water from the leaves. So the higher the VPD, the stronger the pulling force, the higher the transpiration rate will be. That’s an important one to note: the VPD is dependent on the leaf temperature and I think that’s actually a very interesting trend you see, that currently is already happening in greenhouses and I think we’re also moving that in vertical farms – to monitor closely on the one hand the air characteristics, so the air temperature and the relative humidity, but also in the same spot monitor the leaf temperature. And if you do that physically in the same location, you can actually quantify real time the VPD of the crop. And in greenhouses there are already certain algorithms and an autonomous way of growing, to continuously optimize the VPD rather than set a static temperature and relative humidity, which for me I think as a grower is very exciting because that means we’re really focused on the crop rather than on the technical solution. I do find it very important to note that VPD is one part of the equation, but then the air flow, so the impact that the wind speed but also whether it’s laminar turbulence, in combination with the VPD is determining how much transpiration you will have. So it’s not only the VPD itself, it’s the combination of both that we, as a grower, need to evaluate when looking into transpiration rates.
[Keen] Which can also be kind of going into some of the challenges of CEA and the things that make CEA so unique, is the optimal airflow for the plant canopy may not be the same as the optimal airflow for maintenance of temperature and humidity. So then you have the challenges of and importance of airflow distribution and volume in a space.
[Meulendijks] That’s also another thing to really decide in the design stage: do I want air handling and air flow or ventilation combined, or do I do air handling somewhere bring it into the room, and then have a separate system creating airflow that there’s of course the technical decisions that you have to make.
[Keen] It’s one of the things that we get into a lot in mechanical design is CFD analysis which is really identifying what those airflow patterns look like and how to implement them into a mechanical HVAC.
[Atkins] I wanted to add that I just love that distinction between the supply air from the air handlers and then the actual air flow over the crop because often the supply airflow from the air handlers won’t provide enough air movement over the plants alone and so some sort of additional air circulation for movement of the plants is needed, or it can be really helpful.
[Keen] I also like the distinction of controlling VPD. That’s one of the things that we’ve implemented often in control systems is the ability for clients to select a VPD set point and either temperature or humidity, as opposed to just temperature and humidity, so they can actually control to a number of different variables. And I do find – it’s interesting you mentioned that because I just saw that we actually had a question from the audience around that very question around controlling the VPD versus controlling to a temperature or to a humidity. I think that we’ve touched quite a bit on the challenges of CEA. Ian, when you’re looking at load calculations and kind of determining what size does a mechanical system need to be, what are your primary inputs for that, and then once you’ve done that then I’d like for Alberto and Lisanne to chime in on what the additional considerations are beyond just those load calculations.
[Atkins] I guess the first thing we talked about dehumidification often being the driving force, however I always look at lighting probably first in terms of how many kilowatts of light are going into the room, and that just sets the very baseline for the minimal amount of cooling capacity you need. I mean there are some other loads; fans, sometimes your building might not be super well insulated, but primarily it’s the lights. And you just have to make sure you have enough cooling to remove that and just staying on sensible, oftentimes you’ll have enough cooling capacity but you may not have the capacity to get the temperature down as low as you would like it, and so you also have to think about having an air handler large enough to get the temperature down. And then on dehumidification, it’s really how much water is going into the room or is actually really going into the air and it’s been mentioned that that’s a hard parameter sometimes to estimate. I definitely think that measured data is by far the best. There are different equations you can try to estimate that value with, but there’s really nothing like data from a system similar to the one you’re going to be designing. And what I try to do is figure out how much of that moisture is going to the air during the lights on period and then also during the lights off at sort of a peak rate, and then the set points come into play because you have a certain amount of, say, pounds per hour of moisture that you need to remove, but it’s much harder, for instance, to remove that moisture or it takes more capacity to remove it, say, at 70 degrees and 60% humidity than at, say, 80 degrees and 60% humidity. So you have to think about the set points that you’re going to be aiming for in combination with the load. Then going back to something Lisanne said which is that these systems are dynamic, they’re biological, is that these really aren’t constant rates of transpiration you’re getting. Either during the over the growth cycle they change and then they also change diurnally over the course of the day, so you have to have a system that can hit the maximum load and then also the minimum load and modulate all the way between them.
[Keen] So the more granular the cultivators can get on not just volume of water, but what they know about transpiration rates, what they know about actual irrigation strategies and schedules, then the more precise you can be in those calculations. Is that an accurate statement?
[Atkins] Definitely. Though it’s hard to take information, a lot of times people focus on watering when we talk about sizing dehumidification – how much water is going into the room. And it’s true that no, you can’t evaporate more water than it goes into the room, but oftentimes there will be a significant amount of runoff or kind of leg between when water is applied and when it goes into the air, and so like the transpiration rate – the lights turn on and it takes a little while for the transpiration rate to fully wake up, and then the lights turn off and it seems like plants transpire for a little bit right after the lights turn off still before their stomata close. And so the transpiration and how it relates to the plants is a little bit different than just when water is applied, and so I guess I want to make that distinction between watering and transpiration.
[Keen] Alberto did you have anything to add there? What are some of the other considerations when you’re looking at making recommendations for clients, for instance, on sizing systems?
[Lopez] I usually take also, as Ian said, the two main energy fluxes, which is transpiration so latent heat coming from the plants, and then the heat coming from the lights itself. And sometimes in really extreme cases, I take also the conduction from the walls as well, so the energy leaving the walls as well, and then this is all converted into energy. And then that’s the amount of energy that you need to take, or well, you need to take out from the room. So from the perspective of studying transpiration and modeling transpiration, you can separate it in several components I guess the whole conversation that we’ve been having is about, or the final objective of climate control, is basically to steer transpiration. You can steer transpiration and then that’s what you have to do based on the external environment. So we see that most of the facilities have sensors they have all this capability of measuring the environment around the plant. Now we’re seeing more and more sensors dedicated to understanding the conditions from the plant. And then, as Lisanne said, the autonomous growing strategies – they focus more on letting the plant tell us what will be the next move. So I think that’s the point that we are at, or that we can achieve. So instead of measuring the surrounding air or the conditions around the air, you measure how the plant is reacting to it.
[Meulendijks] It’s interesting when you say that, Aberto, on the transpiration rate and that the climate control in the end is all about managing the transpiration rate. I think it’s very interesting to see from an indoor perspective, not being in a greenhouse, to evaluate what are the actual functions of transpiration. And transpiration in the greenhouse or open field has two functions: one being cooling down the crop against excess heat which comes from the heat radiation from the Sun, and the second one is nutrient transports from the roots to the growing parts of the plant. In our situation indoors, it’s very important to note that the amount of heat radiation that’s coming from our light source not being the Sun, but being LED lights, is way lower and therefore also that cooling function of transpiration is way less important for crops indoors. That remains that the main function of transpiration indoors is the transportation of nutrients to the growing part of the plant. And I think where I really would love to get to it with R&D is how can we actually lower transpiration rates to such a level that the crop still has sufficient nutrient supply to these new developing parts, but actually we reduce the latent load inside the room because the cooling effect is much less needed indoors. And also research is still very preliminary, but I think it’s a very interesting opportunity to really distinguish from this indoor situation with much less heat radiation versus greenhouses are open filled with the Sun as a heat source.
[Keen] I think that water management is actually one of the most interesting things about indoor cultivation potentially too. If you can minimize transpiration while maximizing output, then minimize the energy associated with dehumidification, minimize the difficulty of managing your climate, and then potentially recirculate water on top of it, starts to become a pretty compelling argument beyond food security. So it’s a really interesting point in a lot of ways. I was worried we were going to run out of time on this panel; there’s so many more things that I’d like to get to, but I also want to make sure that we get to the audience Q&A, so I think just one more for the panel before we move to the Q&A. Lisanne, what are some of your key indicators of success? What are you measuring, what are you checking to make sure that your climate is well managed, and then once we get there, then Alberto and Ian I’d love to hear from you what you think some of the bigger mistakes that these designers might be making are.
[Meulendijks] So my answer is quite quick and maybe a bit unexpected but it’s leaf temperature. Because I think indoors, we’re putting all this hardware inside of the farm in the end to help the crop grow, and I’m a big fan of really focusing on plant level and the plant itself will tell us a lot. So the combination of the leaf temperature directly related to the air temperature tells me whether or not the plant is transpiring a lot. If the leaf temperature is cooler than the air temperature, that’s the desired situation, and it means it’s transpiring. If it’s not cooler, if it’s the same temperature, then we’re in a problematic situation because that means that my climate doesn’t allow the plant to cool itself down. The other way around can also work. If my leaf temperature is way off, let’s say more than six degrees Celsius lower. That’s really a red flag – it’s like wow, what’s happening here airflow-wise or VPD-wise? So for me, that’s without a doubt the quickest way of assessing how climate is doing. As I understand, it’s somewhat a surprising answer – it’s not related to the hardware.
[Keen] It is, and it isn’t. I mean what it all comes down to is the plant, and so measuring the conditions that the plant is experiencing is really relevant, but it is important, your distinction, between air temperature and leaf temperature. And those are not the same thing – your leaf temperature is generally always going to be lower than your air temperature because of that radio lower because of your transpiration, and higher because of the radiant heat from the light depending on the sense of that light. And it’s not a super straightforward calculation. Ian what do you see with mistakes? Everybody wants to avoid screwing it up, so what are some of the mistakes that you see? And Alberto, I’d love to hear your thoughts on that as well.
[Atkins] As Alberto mentioned earlier, I think designs have come a lot long way in the last several years since I’ve started seeing designs on paper. It’s been mentioned that dehumidification is often undersized during the case of reheat, even more when I see systems that use reheat for dehumidification – they don’t have enough reheat, but I guess another one is that often in vertical farms and especially sometimes lettuce and other crops it seems like people would like to get to really cold temperatures during lights off, a lot of equipment is really not meant to cool below about 65 or 70 degrees Fahrenheit, and what can happen is if it’s not controlled correctly, the DX coil can freeze up, and so one mistake I see is equipment that is applied to try to get temperatures that it just can’t it achieve. And I would say that a similar thing with dehumidification, that often people would like, or in certain types of crops, to get to, say, 65 degrees and a low humidity, and often if there’s a large load that’s not going to be possible without maybe a desiccant dehumidifier. But there’s a cost to that, and so kind of weighing those pros and cons. And then often there’s air flow that hasn’t been thought through in mechanical designs. And then I guess the biggest one just to end on is controls. Some equipment comes from the factory and is meant to control temperature and humidity simultaneously, and sometimes those types of packaged units can work quite well out of the box, but many systems combine multiple pieces of equipment; one piece of equipment for cooling, another for dehumidification, multiple dehumidifiers, or it’s a chilled water system and it’s a whole assembly of chillers pumps, air handlers, dehumidifiers, different things, and so to get all those pieces of equipment working together, to have a smooth control of the system is something that I have seen take a lot of effort. It’s ideally thought about during the mechanical design as well, not as “oh we designed and installed this system, now what do we have to do to control it and have it figured out all after the fact.”
[Keen] And that’s really part of your role, is to make sure that clients understand what they’re getting themselves into with the various technologies that you’re sizing, right?
[Ian] Exactly, to size the systems up front but in a way that will allow them to be controlled and dialed in and operated smoothly.
[Keen] Alberto what about you? Do you see any common mistakes that Ian didn’t mention?
[Lopez] Well, Ian mentioned a lot. At Agritecture, we have this service that is called technical due diligence. So we have to go and analyze all the systems of the facilities, and so what I have is a list of what I have seen in the facilities that I have visited. And one important thing that we didn’t mention is sensor calibration as well. So we rely a lot on sensors and all this type of equipment, but if it’s ill-calibrated or if it’s out of the range that it should be, then all the controls and everything – it’s not operating. And we see this in normally when companies scale up and they go to the 12 or 15 cycle or something like this, and they have been successful in those 12 cycles of production, and then cycle 13 cycle 15 starts having some problems, and everything is on the set point and everything, and then you go there and then you ask for the protocols of calibration of the sensors and they haven’t yet even touched the sensors there – especially the CO2 sensors, those are really tricky as well. I have seen that, as Ian mentioned, from the underdimensioned, obviously you will see a decreasing crop quality, you will see a decrease in all the conditions, you will see an increase in fungi and diseases, all this type of thing.
[…]
[Keen] …calibration, to cleaning, to standard maintenance. That’s going to speak to their ability to properly maintain their climate. It’s also going to speak to an impact the energy that they use over the life of the system. I want to get to some Q&A. Right before we do that, just a little recap: All of these challenges are challenges that Surna is intimately familiar with, and this is what we do every day. So if you are thinking of cultivating or building a cultivation facility, if you have a cultivation facility that needs some correction that you need some help with, reach out to us. Let us help you and if we don’t get to your question, please send it to me after this is over, brandy.keen@surna.com, and I will make sure that you get an answer to your question. One of the first questions that came in that I think is a pretty good one is a lot of times folks might buy a facility that’s already outfitted with a comfort cooling system, and is there anything that a small farm could do without a gigantic investment that might help where they might be able to use a facility that already exists, but use it to cultivate. Ian do you have any suggestions there?
[Atkins] I mean, a lot of comfort equipment can actually work well in indoor grow rooms. Just because it can’t sometimes get to below 65 degrees doesn’t mean it can’t work well to grow plants with. It really depends. Often the comfort systems will just be quite small in comparison to what’s needed for growing, but it could maybe serve the comfort areas of the facility or some small grow rooms potentially.
[Keen] I would say ventilation is probably a relatively inexpensive thing to add. I mean it comes with risks and certainly you wouldn’t have the tight control by relying on ventilation, but that might be something that you could implement while your farm is small until you raise enough money to tighten those things up. A question about reusing removed latent heat in cold climates – Ian, I think that you’ve probably got some experience with heat recovery options and then Lisanne, if you guys have any cold weather tips for capturing and reusing the heat during the dehumidification process.
[Atkins] I think this is where this question is going but, we often recapture heat from the condenser of a cooling system to then use as reheat for dehumidification. So that can be done via hot gas reheat on a package DX unit or with a chilled water system. Heat recovery chillers or water cooled chillers will give heat off of their condenser side and you can use that for reheat as opposed to using boilers.
[Keen] And in an excessively cold climate, which was Lucas’s question, you’re likely to have more luck with that probably the chilled water systems and heat recovery on a chilled water system than with a DX system where you may have more limitation on low temperature operation potentially, but I think that really you’re reusing latent heat in any hot gas reheat system or in any heat recovery system to a certain extent.
[Meulendijks] To add quickly to that Brandy, it’s because the most obvious recovery would be and I think – I still come across systems that don’t have that implemented. It is after the dehumidification step when you have your dry cold air, you do need to reheat it, and ideally you use the heat that was just extracted from your from your air for that reheating step to get to your set point in the climate room again.
[Keen] And that’s a reheat coil on a on a four-pipe chilled water system or on a hot gas reheat DX system, it’s almost an instantaneous reheat or recapture heat. If you want to move it from room to room, I really think the only way that that you can do that without sharing air between rooms would be likely with chilled water unless you’re comfortable with sharing air, which you may or may not be. Lisanne, I’ve got a question: Any suggestions on how we can control the leaf surface temperature without changing the ambient temperature and Rh of the grow room, and do you have any suggestions on the optimal leaf surface temperature for greens? Some of that might be trade secret, so if you can’t answer, we understand.
[Meulendijks] I can answer in that sense that it’s fun biology in a way. So, the answer is controlling VPD and airflow, and so like I mentioned earlier in this in this call, it’s the combination of those two that define, it’s the transpiration rate and the transpiration rate impacts the leaf temperature. So if it’s not the air temperature, we have left the relative humidity set point of the air, but also importantly the airflow across the crop. So in case you have a higher air speed over your crop, you cool down the crop more. On the other hand, plants don’t like to be in a very windy environment – they feel stressed, so they also grow slower. So you see decreased growth rates. But those are the two that you have remaining, so for example if you reduce your relative humidity set point, you get a colder leaf. And if you increase air speed, you would theoretically get a cooler leaf. Deltas, so to look generally what is shared in literature, most of this is still coming also from greenhouses where we have to be careful from translating, but generally a Delta of two degrees Celsius, I’m not sure if we’re talking Fahrenheit or Celsius, but is regarded as like a grower’s objective. However, I do think it’s very important to stress again that it really depends on the technical design, and so it will require experience. Just closely monitor your own crop, and link high quality, high yielding results to measurements you’ve done yourself to verify those numbers as it’s so dependent on in which system you’re growing.
[Keen] Thank you for that, Lisanne. Ian, I’ve got a question for you: how do you decide on the right dehumidification technology? Is there a rule of thumb for when you decide to go from a standard condensate style to a desiccant wheel to…
[Atkins] My broad answer for how to decide on a system type is to just look at the options first and start pricing them out and see which one fits best in the facility. For dehumidification specifically, there’s little standalone dehumidifiers, you can do dehumidification via chilled water / hot water, and then there are desiccants. And desiccants are basically needed whenever you’re shooting for a dew point – and I’m speaking in Fahrenheit – but a dew point below about 50 degrees Fahrenheit is generally in the desiccant range. And then between chilled water / hot water and standalone dehumidifiers, I mean standalone dehumidifiers are great. They work well, sometimes for large facilities it’s just going to require a lot of them, and it can be preferable to use larger air handlers and have fewer pieces of equipment.
[Keen] Okay. And for reference, dew point temperature is the temperature at which water condenses into liquid. And in some cases, your set points may be so low that you can’t get adequate moisture removal because your dew point temperature is too low for a condensing coil. And that’s when you would have to go to a to a desiccant unit. We’ve actually had clients ask for dew point temperatures below freezing, which obviously that can’t happen, so you have to then move to a to a desiccant dehumidifier. So I’ve seen quite a few questions come in about optimal CO2 levels. Lisanne, would you mind opining about optimal levels of CO2 in the space? I’ve got a lot of questions about how often to add CO2 ,but I think the question is really “where should I be maintaining CO2 during lights on and lights off optimally?”
[Meulendijks] Well, let me start with the easiest point. During lights off, no CO2 needs to be added, so ambient CO2 levels are desirable. CO2 is added to the room because we want to enhance the photosynthesis rate, and photosynthesis is the process where the plants actually fixes CO2 from the air into biomass, into the kilograms that we then are able to sell. So it’s a very crucial process, and what we do – we’re actually making some of the glutens plants like providing it an overload of CO2, and it will grow much quicker. It’s important to note that when you increase your CO2 levels, also the optimal growing temperature increases, so there’s quite a lot of literature, academic literature which are available where you see these growth curves where an increase in CO2 from ambient, which is 400 plus, unfortunately but, to 1200 maximum – well that’s a bit like the common boundary that we speak about – and that you really see a large increase in photosynthesis rates which comes at a certain cost, of course. And also, unfortunately the answer is not more straightforward, but it really depends on your facility design how much you do you lose. So if you have a fully closed system, theoretically the only loss of CO2 would be the consumption of CO2 by your plants which you can actually calculate which is your dry matter production of your plant, and then you do the conversions of the chemical molecules.
[Lopez] And to add to that, the benefit that you get from increasing a concentration of CO2 at higher concentrations, let’s say from a thousand PPM to a thousand hundred PPM, is way less that you have if you increase at lower concentrations. So that’s the reason why the curve decreases. What I will suggest is doing an optimization calculation for that to see what will be the actual return on the investment on the concentration of CO2 in your cell.
[Keen] Unfortunately we’re out of time, so for anyone who’s question we did not get to, I do apologize. But like I said, if you’ll reach out to me after the webinar, I will make sure that we get you an answer to your question. Final thoughts from you guys? Lisanne, can we start with you?
[Meulendijks] Yes, I see also still a lot of unanswered questions which I will try to answer in the chat, and in case I don’t manage to, please feel free to reach out via LinkedIn and hopefully I can answer your question. Further, it’s very nice to see that there’s such a lively discussion and I’m very happy to share any more insights on the practicalities of growing indoors. So thank you.
[Keen] Thank you Lisanne! Ian?
[Atkins] Well thanks everyone for attending the webinar. I really enjoyed the discussion. If there’s anything that you’d like to reach out to me about, you can find me on LinkedIn and reach out to me there.
[Keen] Thank you so much Ian! Alberto?
[Lopez] Just send those questions I will try to answer as much as I can – and I just want to thank everyone for joining the webinar and really interesting questions I’m reading.
[Keen] Feel free to reach out to all of us LinkedIn, direct email, and if we can help, we certainly will. I appreciate everyone joining us today, thank you so much!